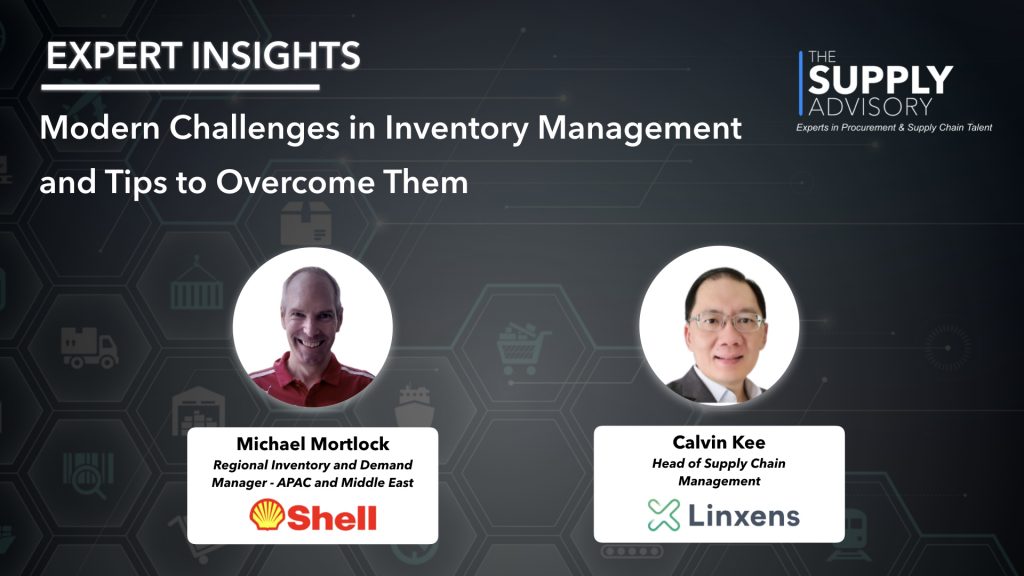
Inventory management can eat up a large chunk of a company’s operational cost. That’s because it comprises several parts like managing costs of storing excess items in warehouses, dealing with obsolete inventory, and deciding whether to switch to a just-in-time inventory management model.
It also sits at the heart of business growth and development, pushing supply chain leaders to devise sound strategies to control available stocks and satisfy the current market demands. Leaders actively mitigate inventory management issues before they can leave a massive dent in their operations and expenditure.
Without careful planning, a small problem can quickly cascade into something bigger and more complicated. Some examples of these inventory management failures include the following:
- Nike’s inaccurate inventory forecasts led to a $100 million revenue loss in the early 2000s
- Ralph Lauren’s inventory system error plummeted their profits by 50 percent back in 2016
- Target’s several inventory management and logistic mistakes caused them to abandon 133 store openings in Canada
- The 1999 Hershey’s meltdown when the company failed to supply over $100 million worth of chocolate for Halloween
Undeniably, a lot has changed in the way inventory management gets handled in organizations. Technological advancements have paved the way for automation and a significant reduction of human error. Supply chain leaders have found better ways to avert inventory management disasters by integrating tech solutions.
So now I wonder, do companies still have the same set of inventory-related problems, or are there new and more complicated tasks at hand?
To help us understand the inventory management landscape a bit more, I have reached out to two Supply Chain Leaders, Michael Mortlock from Shell and Calvin Kee from Linxens Singapore to share their insights on the question:
What are the Top 3 challenges that you face as Supply Chain Leaders in Inventory Management and tips to overcome each of those challenges?
Kindly scroll down below to read their response.
Michael Mortlock
Regional Inventory and Demand Manager – APAC and Middle East
Shell
1. Fluctuating Demand
Over the last 18 months, we have seen demand fluctuate more significantly than ever before with huge runs on some products and drying up on others. Supply chains heavily invested in being lean were heavily hit by this and there has been a requirement to pivot to more agile and flexible modes of supply in order to continue to keep an acceptable balance between service and inventory levels.
This has also exposed where supply chains are not well aligned – especially gaps in strategies between customer and vendor where the customer might be agile, but cannot deploy this agility because key vendors are running lean.
2. Ensuring Accuracy of the Key Parameters
The same fluctuations mentioned above have also made relying on historical information and trends a risky proposition. This makes not only forecasting difficult but also calculating the correct amount of safety stocks, lead times and ordering lot sizes very difficult.
To ensure this accuracy in these key parameters, additional effort and collaboration (with Sales teams, customers, and vendors) are required to cleanse historical information and align on what are future expectations that will drive variability and cost in the supply chain.
3. Lean vs Agile
Overall, the last 18 months have forced a significant change on much of the global supply landscape, and this may become the “new normal” at least for the medium term. Both local and international logistics capacity, cost, and reliability have all changed. In many industries, the availability of supply of parts and raw materials has shrunk due to reduced capacity or the number of vendors.
In response to these factors, organisations need to reassess not only their supply models (lean vs agile) but also the amount and location of inventory held to support the level of service required by the business. With so many inventory-related parameters changing so quickly, inventory reviews need to be quick and frequent to continue to ensure the right product is in the right place at the right time.
Calvin Kee
Head of Supply Chain Management
Linxens Singapore
1. Supply Chain Visibility
Disruption in raw material happens more frequently and with a more severe impact in this period. COVID-19 affects manufacturing operations in ways like “lockdown” causing factories to stop production totally or having to operate with less manpower affecting their final output. Also, the trickling effect of the Suez Canal incident, shortage of containers, jams at seaports and airports do not help to make sure the supply of material can arrive on time as planned.
Hence, improving the visibility of inventory at suppliers and their 2nd or 3rd tier suppliers is important. Early signal and anticipation of any delay will help the downstream supply chain to respond and re-prioritize promptly. The application of new technology in logistics tracking will play a key role in success.
2. Supply Chain Partnership
During a crisis, demand becomes volatile and at risk of causing a “bullwhip” effect because customers tend to stock up in short term. Normally, a monthly SI&OP (Sales, Inventory & Operations Planning) cycle is sufficient for inventory planning. In the current situation, more frequent updates and tweaks become necessary in between the monthly cycle. As a result, partnership and closer communication with up and downstream of the supply chain will help to derive a win-win solution.
3. New Normal “Just in Case”
Lean practices have been applied in inventory management for years. Particularly, JIT (Just In Time), to optimize and right-sizing inventory levels at various nodes. However, in view of potential shipment disruption and unplanned production stoppage, “Just In Case” is becoming the new normal. This means selectively increase the level of Safety Stock and keeping the stock physically closer to point of usage. A fine line needs to be managed between inventory and the cost of urgent expediting.
—–
Indeed, a lot has happened in a span of a few years in inventory management. The global crisis has also pushed this function to its limits, as organizations have to find ways to juggle inventory-related concerns, tightened lockdown policies, and limited availability of supplies and workforce. In addition, inventory management leaders need to act in response to the current supply fluctuation and market demand, and the constantly changing KPIs.
By having a full grasp of these issues, inventory management functions have a better shot at managing issues and planning necessary contingency plans. We hope our discussion has shed light on the current challenges in inventory management.
Again, we would like to extend our warmest gratitude to our generous guest contributors for this month’s Expert Insights. Thank you Michael and Calvin for sharing your insights on the given topic.
And for those who want to learn more about the latest news, updates, and insights on supply chain management and procurement, be sure to subscribe to the Supply Advisory newsletter.
Ananya Sinha Roy is the Director at The Supply Advisory, a leading executive recruitment firm specialising in Procurement & Supply Chain.
You can view the The Supply Advisory website or contact them directly at info@supplyadvisory.com for a more detailed discussion.