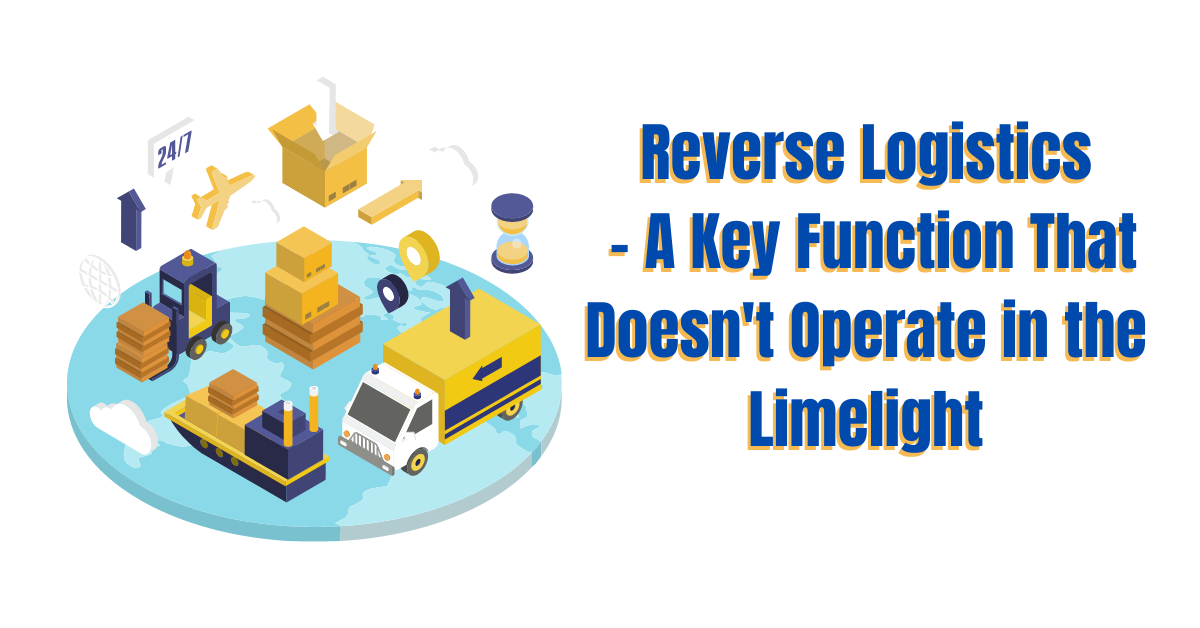
Everyone has their fair share of binge-shopping on items like a pretty dress or a random gadget that’s supposed to take your baking to Mater Chef level. I bet that you also had several instances when you had to return things because of various issues like a damaged or wrong item. Have you ever wondered what happens after you ship things back to the sender? How extensive is the process? Moreover, what reverse logistics challenges do companies deal with each time consumers request to return their purchases?
Challenges in Reverse Logistics and How Companies Cope
Reverse Logistics Problems Today
Indeed, the rising popularity of eCommerce has brought in millions of revenue to retailers and manufacturers worldwide during the last few months. However, the upward trend of the eCommerce industry has also reminded us of one of the biggest problems in supply chain management – handling reverse logistics.
It’s no secret that reverse logistics is costly and labour-intensive. It also impacts various aspects of a company’s supply chain. Notably, besides eCommerce and retailers, other sectors also grapple with the immense challenges that come with reverse logistics. In my blog below, we will explore the different challenges and how companies cope.
Challenge #1: Dealing with the Returned Items
Compared to traditional stores, eCommerce has a higher product return rate at around 30 percent in some of the popular categories. In 2020 alone, UPS reported about 1.9 million eCommerce returns for online retailers in the US. European retailers also faced a similar dilemma as their return deliveries cost increased from $234 billion in 2015 to $388 billion four years later.
Good thing, many eCommerce platforms and retailers have been successfully tackling eCommerce return challenges using tactics like:
- Investing money on tech solutions such as to reduce returns
- Tapping into re-commerce companies which serve as liquidators for resale to consumers
- Partnering with 3PLs that provide complete solutions for returns management and storage
- Utilizing smart IoT devices for remote repairing or troubleshooting a product
Challenge #2: Risk and Logistics Management
Besides dealing with returned items, many also struggle with problems concerning risk and logistics management. This is especially true for companies that need to ship back hazardous waste materials (HazMat). In such cases, certain regulations on the quantity of the HazMat to be shipped, shippers used, and the packaging exceptions.
Apart from the risks of transporting hazardous wastes, others also tackle other problems such as labour strikes or weather disturbances. Then, there’s also the possibility of transportation delays like the incident in the Suez Canal, which affected the transport of more than $10 billion worth of products each day.
To cope during these situations, businesses usually utilize techniques such as supply chain modeling. SCM leaders often don’t have the luxury to handle issues one at a time, so it becomes extra crucial for companies and functions to carefully plan every aspect of their SCM models.
Challenge #3: Controlling the Costs and Resources involved in Reverse Logistics
As we have pointed out earlier, reverse logistics comes with huge costs. Besides the expenses incurred in sending back items, organizations also have to factor in the costs of other things like repairs, air/sea freight, warehousing, and reselling. The longer products stay in the reverse logistics channel, the higher the costs can get.
To cope with this challenge, businesses usually collaborate with an established logistics partner with the technology and infrastructure needed to regulate costs and improve customer service. Others use additional techniques to manage their expenses and resources for reverse logistics, such as:
- Leveraging forecasting programs for product returns and sales
- Remanufacturing/Refurbishing obsolete products so retailers can resell them
- Combining delivery and pickup to improve efficiency and minimize costs for large items such as televisions and pieces of furniture
Challenge 4: Managing the Different Stakeholders Involved
It takes time to complete the processes involved in a typical reverse logistics pipeline. It involves the collaborative work of various functions, including customer service, repair technicians, manufacturing or supply chain departments, and more. Additionally, some may have to deal with contractors and dealers for the supplies needed in replacing defective parts of items like laptops, phones, cameras and other gadgets or tech equipment.
To succeed in this particular challenge, businesses and reverse logistics leaders may need to pay close attention to the interaction between the different stakeholders. It could be done using a manual process or a computerized program, depending on the systems in place.
The Supply Advisory and SCM Recruitment
The challenges in reverse logistics will undoubtedly keep coming as the demands for eCommerce and other industries keep on growing. Surely, companies, no matter the size or scope, will continue to look for ways to innovate and rise above the situation with the help of the right team.
If you’re looking to expand your SCM workforce that will focus on reverse logistics, or if you need people to fill vacancies in a reverse logistics function, we can help. We at Supply Advisory offer holistic SCM talent acquisition solutions tailored to the needs of your organization. Contact us today for more information!
Ananya Sinha Roy is the Director at The Supply Advisory (a division of Datasearch Consulting), a leading executive recruitment firm specialising in Procurement & Supply Chain.
You can view the The Supply Advisory website or contact them directly at info@supplyadvisory.com for a more detailed discussion.